The 10 Things You Need to Know to De-risk Solar O&M – #6: Measure What Matters
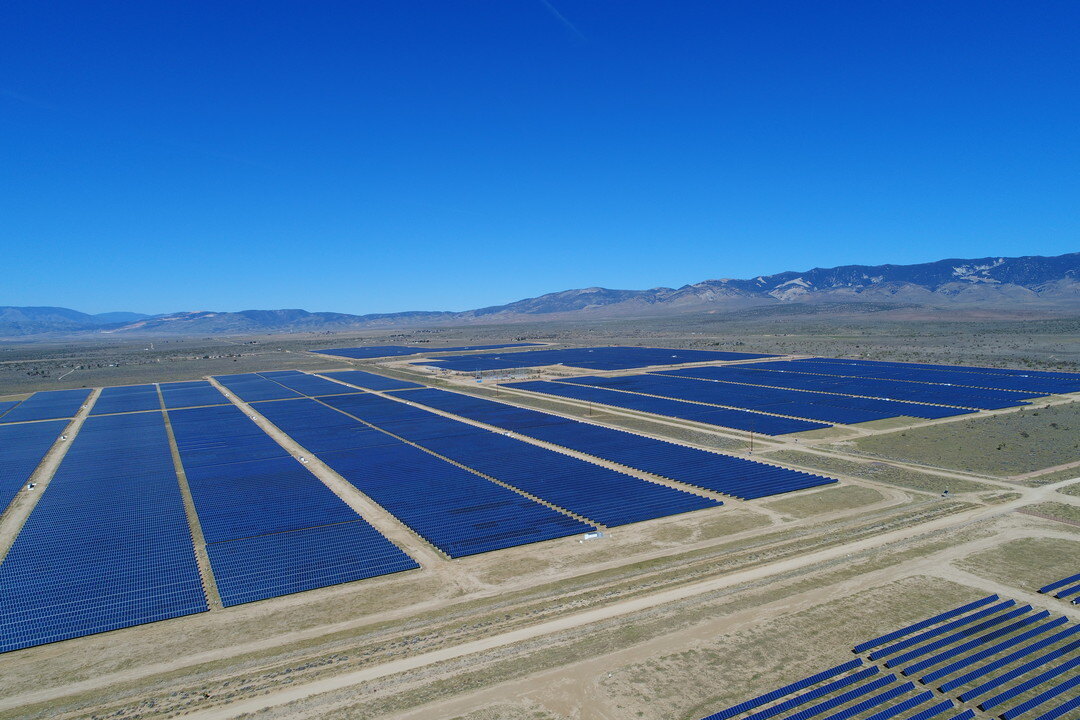
Stay in touch
Subscribe to our newsletter for expert insights, company updates, and the latest in renewable energy management solutions.
HOW AM I DOING?
Why is it that so few project owners can honestly answer the question “how well are your solar assets running?”
Though the solar power industry is relatively young, it should be mature enough to reliably measure plant performance. While many project owners can provide general measures of plant performance like “the fleet is running at 98% availability…”, or “all our projects are meeting their cash flow forecasts…,” few can provide detailed analyses. For example, if asked, “are you using a capacity-weighted availability metric?” or “how much margin is included in the project cash flows numbers?” you either get a blank stare or a quick change of the subject.
So how do we know if our plants are doing as well as they could?
WHAT TO MEASURE
When we think about what needs to be measured to determine if our solar project is performing well, we should consider at least the following five categories:
- Safety
- Operational performance
- Reliability
- Maintainability
- Financial performance
Though a safe performance record is of utmost importance, I will not address that metric in this paper so let’s look at the other four.
OPERATIONAL PERFORMANCE
Operational performance measures how well a plant is converting the available solar resource into electricity. In other words, we are measuring the plant’s electric conversion efficiency. If setup properly, conversion efficiency is a good measure of operational performance because we can use it to trend a plant’s health over time and to compare a whole portfolio of plants against one another. Though Performance Ratio (PR) is often used for this purpose, we recommend using the Performance Index (PI) metric instead. Performance Index is the ratio of Actual-to-Expected production of the system. A PI of 100% means that the solar power system generated all the energy expected of it during the reporting period.
There are a few reasons using Performance Ratio as in indicator of performance is not optimal. First, Performance Ratio values are relative to plant design. A plant may have a higher Performance Ratio than its neighbor even though it is performing worse than its neighbor simply due the design of that plant.
Secondly, Performance Ratios are often not weather-corrected. The Performance Index metric, however, is always weather-corrected. We weather-corrected PI when we calculate its denominator, Expected Energy. To do so, we recommend using the regression method described in the ASTM 2848 standard to calculate the real-time weather-corrected Performance Index for each plant. Once these conversions have been made, you can trend each plant’s Performance Index over time to track overall system health using a robust monitoring system.
RELIABILITY
Reliability is a measure of a system being available to perform its intended function over time. For a solar power plant, the best metric to trend is Equivalent Availability Factor, or EAF. EAF is the ratio of the Actual to Potential Time that the system generated electricity at its expected capacity. Most solar operators track Availability Factor, but not Equivalent Availability Factor. The equivalent part of EAF modifies the availability factor to make it capacity-weighted. In other words, “was the system running at its full and unrestricted capacity (kW) every minute it was available to generate?”
By not only evaluating if the unit is running, but is it operating at peak performance while it is running, we can truly determine if the system is reliable in all its components. If the solar industry reported Equivalent Availability Factor instead of the simple Availability Factor (AF) metric, I am quite sure that the reported value would be meaningfully lower than the 98% typically touted in the industry.
MAINTAINABILITY
Maintainability is the probability of performing a successful repair action within a given time. Where Reliability is a measure of time-to-failure, Maintainability is a measure of time-to-repair. Maintainability must be designed into a plant. You can have a plant with good operational performance that was not thoughtfully designed for maintenance and quickly get into big trouble. For example, I have seen plants that required a crane to lift the inverter enclosure for even minor repairs because insufficient clearances were designed-in place for personnel access.
Similarly, some inverter and transformer parts are so difficult to source that I have witnessed equipment outages lasting months until a part was finally located. Severe negative impacts to project cash flows resulted. Two important Maintainability metrics that you would do well to track are mean-forced-outage duration (MFOD) and mean-time-to-repair (MTTR). These metrics provide insights into equipment maintainability and the ability of your field service team to quickly service plant equipment.
FINANCIAL PERFORMANCE
Of course, solar power is more than just a good idea and a responsible way to generate electricity. It must also be an investment that attracts project capital. Our recommended financial performance metric for a solar project combines the best of operational performance, reliability and maintainability into one factor: the Commercial Availability Factor (CAF). Commercial Availability Factor is the ratio of Actual-to-Expected project revenue. The numerator for the CAF metric is Actual Energy Revenue generated for the period. The denominator for the CAF metric is Expected Energy Revenue generated for the period, where Expected Revenue is the product of Expected Energy and the time-of-use energy rate for the site.
A CAF of 100% means that the facility has generated the totality of all energy revenue it could have produced given the actual solar irradiance of the site for that period. Note that this is not the same as the “modeled”, “budgeted” or “forecasted” revenue for the period. Surely, we also need to measure actual vs. forecasted revenue for investor reporting, however, the problem with only tracking actual-to-forecasted revenue is that forecasts are always wrong.
Forecasts are “wrong” for the following reasons:
- Forecasted weather is never the same as actual weather so we are using an improper measuring stick when comparing actual-to-forecasted revenue. A plant can exceed forecasted revenue for the month and at the same time leave substantial money on the table
- Forecasts are usually built on margined performance models, which means they underestimate the actual production capability of the plant
- Bank engineers often add a “haircut” to the plant performance model to de-risk achieving project returns
Commercial Availability Factor removes all the noise from the evaluation by comparing actual revenue to optimal revenue given the plant’s actual performance capability and actual weather.
Commercial Availability Factor should be considered the holy grail of solar project financial performance. Owner’s armed with this information are truly “measuring what matters.”
HOW TO SETUP FOR SUCCESS
We don’t have space available in this paper to discuss how to fully setup these metrics for your solar portfolio, however, the following are a few high-level keys to success:
- A scalable, real-time monitoring system that can ingest high frequency data from all your plant data systems and populate a unified, contextual time series historian
- An Event Manager that overlays the plant data layer with full data curation to ensure high quality, validated inputs are used in the generation of the performance metrics
- A library of industry-standard calculations and algorithms need to be applied to every data set so standardized and aggregated performance metrics can be applied consistently across the fleet
- A set of normalized performance metrics that are trended over time to allow comparison with Expected values. Control limits need to be set so the appropriate parties are notified when trigger values are exceeded
The above requirements dictate the use of an “industrial strength” data platform that integrates production, maintenance and commercial management data into one unified system. If you are serious about achieving full financial performance from your solar assets, you will be willing to make this investment.
Next week, in lieu of our regular weekly article, please join me in Anaheim at the Solar Power International conference where I am part of a panel highlighting: The 4 Things You Need to Know When Designing a Comprehensive O&M Budget for Commercial, Industrial, and Small-Utility Projects
- Tuesday, September 25, 2018
- 4:00 PM – 5:00 PM
- Location: 205AB
To set up a meeting or connect with me or Power Factors at #solarpowerinternational, please contact us at info@pfdrive.com or visit our website www.pfdrive.com to see a full calendar of events.
HOW TO CALCULATE BREAK-EVEN TRUCK ROLL COSTS
To calculate break-even truck roll costs for your organization, you will want to factor at least the following items into your analysis:
- Average distance to project location
- Average number of technicians required
- Fully loaded base labor rate – should include benefits, cost to train and fully equip with tools and PPE
- Technician utilization rate – billable hours divided by potential work hours
- Amortized vehicle expense rate – lease, fuel, insurance and maintenance
- Other costs – if air travel and lodging is required, include those costs per trip if they are not fully reimbursable
Ultimately, we want to know the average cost per truck roll in dollars per site visit of non-reimbursable costs. You may want to further categorize truck roll costs by distance:
- Local (less than 20 miles or 1 hour by vehicle)
- Regional (more than 1 hour, by vehicle)
- Overnight (requires non-reimbursable air fare, lodging or extended vehicle travel)
Let’s assume you generated the following truck roll costs for your organization for one of your service regions:
- Local – $125
- Regional – $400
- Overnight – $1500
Therefore, unless you have service level agreement penalties or some other disincentive, you would not perform an overnight corrective maintenance task like resetting an inverter until your break-even accumulated lost revenue was greater than $1500.
For example, if a remote (overnight) plant lost a 500 kW inverter for a project with a PPA price of $0.10/kWh, you would be losing about $180 per day. Therefore, your recovery period for a $1500 truck roll would be about 8 days. If your field service team is fully loaded doing cost effective maintenance elsewhere, you are better off deferring the maintenance for a week or so until you can group it with other work in the area.
SUMMARY
Scheduling corrective maintenance for the solar asset class needs to be evaluated using a different paradigm than traditional and wind power assets. Having equipment event data sorted by opportunity costs to compare with truck roll costs is essential for running an economic fleet. Power Factors’ performance management software platform provides this kind of real-time visibility into operational performance and equipment maintenance translated into dollars, so the right economic decision can be made.
Next week we will address the topic of having a well-defined service delivery model. As always, your feedback and insights on these important topics are appreciated.
*Note that this paper is written from the perspective of the plant owner. If the operator does not have aligned incentives with the owner, opportunity costs may be different and mis-aligned with the owner’s.
Steve Hanawalt is Executive Vice President and Co-Founder of Power Factors LLC