COVID-19 Impacts on Solar O&M — Solar Maintenance: Social Distancing, Site Access and Other Impacts
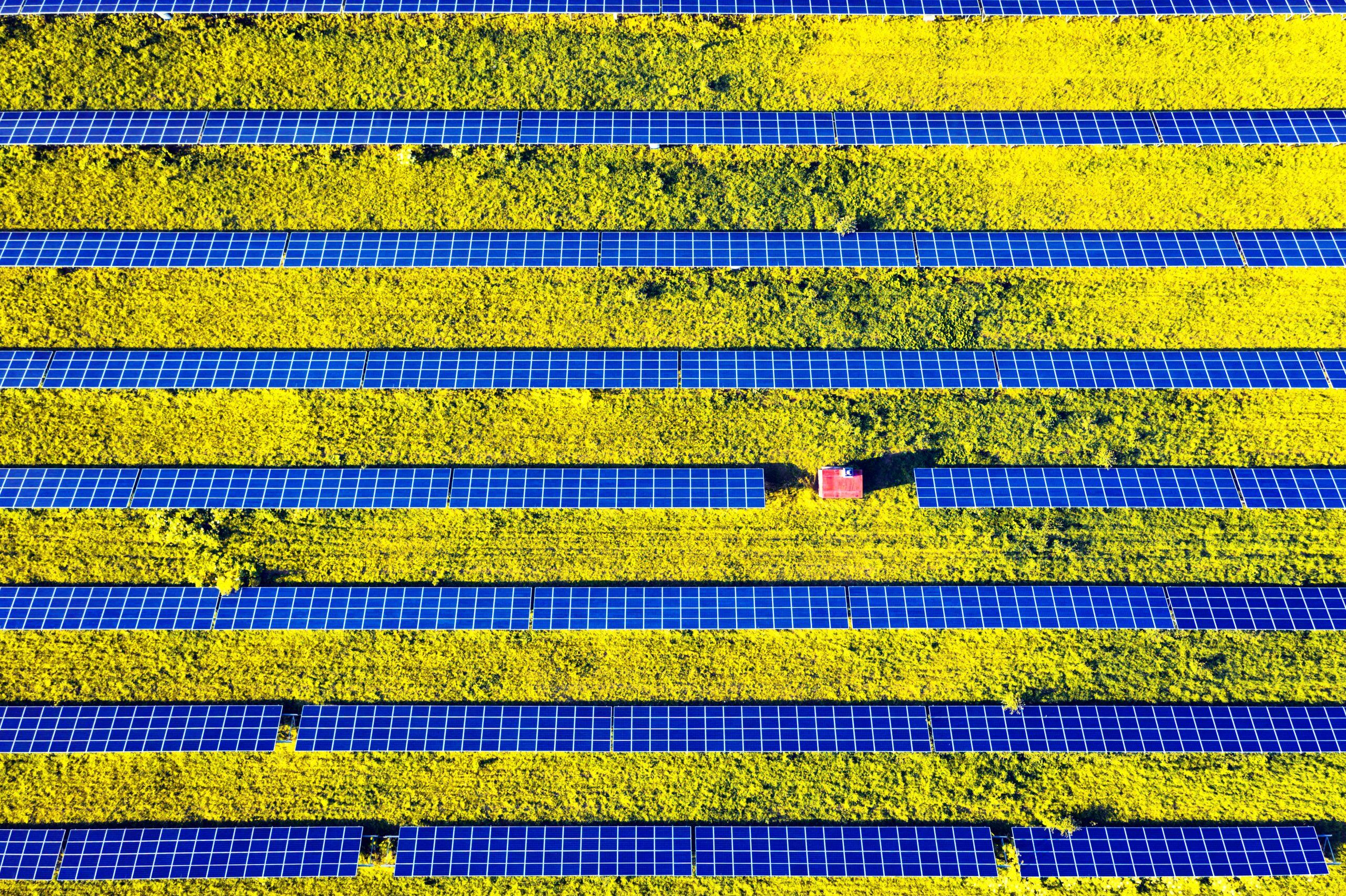
Stay in touch
Subscribe to our newsletter for expert insights, company updates, and the latest in renewable energy management solutions.
In my last article, I covered some of the ways that the COVID-19 pandemic is impacting access to spare parts for solar projects around the world. In this week’s article, we will explore how the pandemic is affecting solar project maintenance and things you can do to mitigate that impact.
Never forget that COVID-19 is first and foremost a human issue—energy production and profits take a back seat to personnel safety. All maintenance decisions start with this core value.
EMPLOYEE EMPOWERMENT
Since personnel safety is the ultimate decision-making criteria, once a decision has been made to dispatch someone into the field, that employee must be empowered with the final authority to decide to perform the work—or not.
Empower people to make the real-time call when it comes to health and safety. This requires leaders who demonstrate that people are first priority through their actions — not just their words.
If, in the judgment of the worker, the travel or site conditions put them in a position of unacceptable risk, they should be able to pull the plug on the maintenance activity with no negative consequences.
It’s been said that, in organizations, “culture flows downhill.” If senior management gives health, safety and employee empowerment only lip service, everyone in the organization knows. Make sure these company values are more than just posters plastered up on office walls and promptly ignored.
DG VS. UTILITY MAINTENANCE CONSIDERATIONS
What can solar operators do to maintain employee health and safety during these challenging times? First, let’s go over some key differences between DG and utility sites that should be considered.
When reviewing maintenance best practices during the pandemic, operators report that maintenance had been more negatively impacted at their distributed generation (DG) sites than their utility-scale solar sites.
Here’s why:
- Utility sites are usually larger and more spread out, allowing easier adherence to social distancing standards than DG sites.
- Utility sites are typically in more isolated locations, so technicians are less likely to need to prepare for interactions with the general public.
- Local technicians usually staff utility sites, while DG technicians often travel long distances to get to the job site. (On a separate but related note, one industry colleague confided that the stress of being away from family, living in hotels and subsisting on fast food was wearing on their team of DG technicians.)
HEALTH AND SAFETY BEST PRACTICES DURING THE PANDEMIC
Important note: I’m writing based on the best information we have today, April 9, 2020. However, given that new data still is emerging regarding how coronavirus spreads, it’s incredibly important to consult official sources for the most accurate and up-to-date information (such as the CDC, FEMA and https://www.coronavirus.gov/).
SOCIAL DISTANCING
Government guidelines around safety practices for workers must be adhered to at the job site. As discussed above, requirements such as social distancing are usually easier to adhere to at utility sites. Most maintenance tasks don’t require people to maneuver in close quarters.
You might need to think about deferring work or revising work methods.
Still, constant spatial awareness is key to keeping six feet of distance between individuals during maintenance work. This may mean that inverter enclosure and other confined space work needs to be modified, for example.
For some space-constrained DG sites, maintaining social distancing requirements can be more difficult. Special precautions should be taken to practice social distancing and wear masks when performing tasks in these environments. If the work does not allow this, decisions will need to be made about deferring the work or revising work methods.
HYGIENE
Needless to say, proper hygiene is extremely important. It is believed that the coronavirus can survive up to 72 hours on hard surfaces. Cleaning doorknobs, surfaces, panels, latches and all other surfaces workers touch before and after maintenance with a good antibacterial wipe is a must.
SINGLE-USER TOOLS
Most PV technicians have their own tools and tool bags as a standard practice; however, more expensive specialty tools are often shared. Technicians should not be sharing tools during the pandemic.
If there is a tool that must be shared, like an I-V curve tracer, it’s imperative to take the extra time and care to carefully wipe down the entire tool after use and to wear single-use surgical gloves while using and cleaning the tool.
ACCESS CONSIDERATIONS
SITE ACCESS AND SCREENING
As discussed in my previous article, access to many DG sites is now more difficult or impossible. One operator told me that many of their DG hosts are not returning their calls. Often, no one is at the site or, if some people are, they aren’t allowing anyone else on site – even in the case of a system outage.
Access to sites might be impossible, delayed or limited. Prepare for this possibility by building in extra time for things like additional screening practices.
Other sites are allowing access but have instituted additional screening practices, slowing the process. Because PV maintenance is considered part of the critical infrastructure of our energy grid and PV technicians are considered essential workers, site access is usually given.
ACCESS TO SPECIAL EQUIPMENT
So far, access to special equipment used in PV maintenance, such as scissor lifts and cranes, has not been a problem. However, as the pandemic worsens, we can expect that this will be a problem in some areas.
For example, in California, all non-essential construction services have been shut down through May 3rd. Equipment rental companies may similarly shutter their business until this restriction is lifted and access to equipment rentals will be affected.
BLOCKADES AND ACCESS TO VENDOR SPECIALISTS
For the most part, blockades of ports and international checkpoints have not affected PV maintenance with the exception of countries that have been forced to essentially shut down their borders, such as Italy and Spain.
I expect this might become more common as COVID-19 infection rates grow in other countries. Border closures could make access to OEM-certified technicians more difficult. This creates a problem, as many in-warranty maintenance and repair tasks must be completed by an OEM-certified technician.
Start having conversations with your key equipment suppliers now about the possibility of having non-OEM technicians conduct in-warranty repairs.
One colleague told me that this problem should be mitigated by the recent trend for these vendors to allow non-OEM technicians to perform in-warranty maintenance and repairs if they have adequate training.
I recommended that you have these discussions with your key equipment suppliers before you need them so you can have contingency plans in place should the need arise.
COLLABORATION WITH OTHER OWNERS
I know this may come as a strange idea to my solar industry colleagues, but have you ever thought about collaborating with other owners during these difficulty times?
My career started in the gas-fired IPP industry almost 40 years ago. For the first ten years of the industry we never shared information with other owners for fear they would steal all our proprietary ideas. As the industry matured, we learned that a better model is to form user groups and share best practices.
Over the past 40 years, I’ve witnessed how collaboration with colleagues adds value for all and strengthens the industry as a whole.
“A rising tide lifts all boats” is a general truth that I have seen work in the energy industry. Now is the time to start having meaningful conversations with others in the industry, and to think about sharing parts, people and know-how. My experience has been that you get back more than you give away in these encounters.
DEFERRING PREVENTIVE MAINTENANCE
I am hearing a lot of owners and operators agreeing to defer non-critical preventive maintenance (PM). This is especially true for DG sites where access can be closed or very restricted.
Some owners are shutting site gates and allowing only employees to access their sites. We won’t know the long-term maintenance impacts for a while; however, my guess is that if the crisis only lasts a few months, the impacts will be small.
Use this as an opportunity to work towards condition-based maintenance. We need an agile and resilient service delivery model.
This is because calendar-based maintenance intervals tend to be conservative in the first place; if an operator has good remote monitoring diagnostics, the machine will inform the operator if it’s time to perform maintenance.
My recommendation is to use this time to work towards a more condition-based monitoring regime. If this pandemic is teaching us anything, it’s that we need a more agile and resilient service delivery model for maintaining our solar power plants.
DEFENSE IN DEPTH
Over the past few weeks, I’ve had the honor of speaking with some of my colleagues who used to work in the military and who now work in the solar industry. Their training around how to respond during a crisis has been incredibly insightful.
One military practice that I found particularly applicable now is the idea of “defense in depth”— building layers into your support structure to so you have the wherewithal and flexibility to address future unknown variables.
How can we build resiliency into our operations so we’re better prepared next time something unexpected happens?
An idea for implementing a “defense in depth” plan for solar O&M is to cross-train workers so they’re capable of filling in for various roles. Once trained, remove them from the front line unless or until they are needed.
For example, you might train a performance analyst how to do Level 1 monitoring in a remote operations center (ROC) for a week, then remove them from the ROC to work from home. Or you could train an operations supervisor to do basic site maintenance tasks — like inspections — and then send them back home.
This way, if one of the shifts in a ROC has an outbreak of coronavirus and needs to be quarantined and cared for, you’re able to bring in the performance analysts to cover that shift, and so on.
This kind of resiliency in our O&M practices needs to be in place before the next crisis hits so we can adapt quickly to the circumstances and “keep the lights on” as solar power continues to grow as a major generation source on the grid.
SUMMARY
The impact of the COVID-19 pandemic is being felt in solar power facilities across the globe. But there are adjustments you can make to your O&M service delivery model to better protect your employees and increase your maintenance organization’s resiliency.
Most of these adjustments have to do with better collaboration among employees and industry partners as well as the adoption of new technologies. I encourage you to think differently about your approach to solar O&M over the next few months and to be open to change.
May you and your loved ones stay safe and stay well!
Special thanks to industry experts, including Mike Eyman, General Manager of Origis Services, for their insights into how to manage O&M in these challenging times.
Steve Hanawalt is Executive Vice President and Co-Founder of Power Factors. Follow him on LinkedIn for more industry insights.