[ARTICLE 3] WHY YOU NEED AN INTEGRATED APM TO MONITOR OPERATING COSTS
Energy storage introduces financial risk to hybrid renewable power projects due to uncertainty about the true cost of lifetime operations.
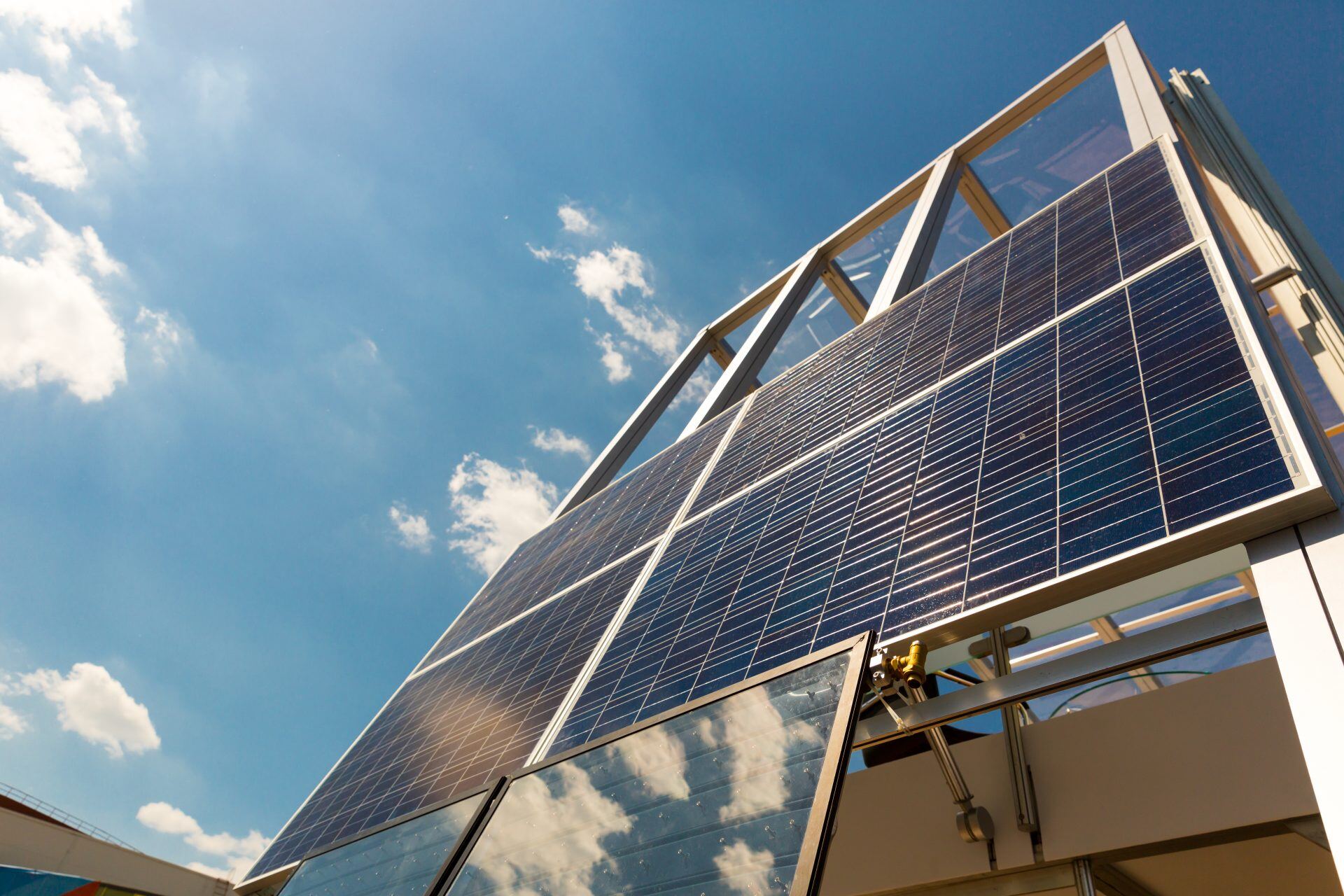
Stay in touch
Subscribe to our newsletter for expert insights, company updates, and the latest in renewable energy management solutions.
This is the third article in a four-part series about the unique O&M challenges of the energy storage asset class and the reasons why owners and operators of mixed portfolios of solar, wind and energy storage assets need an integrated asset performance management platform.
In the previous article in this series, we discussed how the battery storage asset class introduces financial risk to hybrid renewable power projects due to uncertainty about the true cost of running this asset over the life of the project.
The two major factors that create this risk are the lack of historical operating data from which to assess operating costs and the uncertainty around how the asset will be cycled. As we discussed, a battery energy storge system (BESS) may last 2 years or it may last 10 years depending on the severity of the equipment operating duty.
And, unlike the typical solar or wind project, where the operating duty is largely known in advance of commercial operation, most storage systems’ operating duties will only become apparent as future energy prices and price volatility occur over the next few decades—and no one can predict what those price strips will look like in advance!
So how can the owner of a hybrid renewable portfolio manage this risk? Well, the key to managing risk is to better understand it and reduce its uncertainty. If we are going to better understand the operating cost uncertainty of a battery storage system, we need to mine its historical operating data and correlate operating duty with equipment reliability and cost.
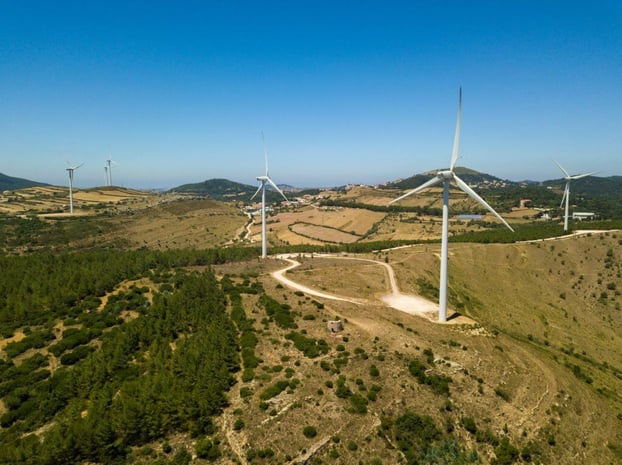
Understanding how operating costs vary with equipment operating duty will provide deep knowledge into the asset’s true operating costs and allow us to make good projections about future operating costs.
I proposed in the previous article that using traditional disconnected monitoring, maintenance, and asset management system data platforms to generate this information is a suboptimal approach and that an integrated platform approach is needed.
In this article, we will talk about how an integrated data platform can be used to calculate the true cost of O&M for the hybrid renewable power plant and how this information can be used in the project economic model to ensure the storage system is optimally dispatched now and in the future.
OPERATING COST DATA SOURCES
Before we discuss operating costs, we need to revisit the concept of an asset’s “equivalent operating hours” that I introduced in the last article in this series. Equivalent operating hours differ from equipment clock hours in that they normalize equipment run data to account for the severity of the operating duty. Correlating equivalent operating hours to operating costs informs the owners if the cost of the cycle is exceeded by the revenue gained from the cycle.
What operating data do we need to understand storage system operating costs and equivalent operating hours and what data sources can be used? Let’s review each data type and where the data comes from:
MAINTENANCE SYSTEM DATA
The maintenance system (EAM or CMMS) is the system of record (SOR) for all things related to scheduled and corrective equipment maintenance. The work order and asset registry are the heart of the system, and it is in these modules that we record transactions of the physical maintenance performed on the equipment.
Though the financial system should be the system of record for labor and material unit pricing, the maintenance system is where we record the frequency and volume of labor, spare parts, tool and equipment rental costs associated with maintaining the plant.
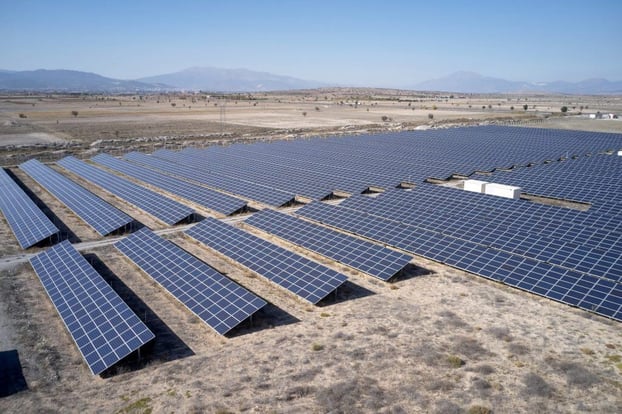
It is important that there is enough detail in the work order records about the craft(s) that performed the labor, how much regular and overtime labor was performed, and how much material and related equipment is used in the maintenance activity.
In addition, it is important that the costs of both internal workers and contractors are recorded. To truly understand the cost of a renewable energy asset relative to its operating duty, we need detailed information about the maintenance activity that resulted from specific dispatch scenarios.
This is why integration between the maintenance system and the monitoring system is so important. If these two systems are not talking to each other, it will be very hard to correlate operating costs with equivalent operating hours.
Separate data systems may be able to tell you on a macro level that you spent this much money maintaining the system relative to these operating hours, but they won’t be able to associate varying operating duties with costs – which is the data you need to manage future costs.
The following are some of the data sets that should be recorded in the maintenance system:
- Labor, materials, equipment rentals and other consumable quantities used in the maintenance activities
- Corrective and scheduled maintenance performed with a detailed categorization of standardized work tasks
- The failure, cause and action code associated with corrective maintenance and any associated monitoring system event records including device-level fault codes
MONITORING SYSTEM DATA
The monitoring system is where we track equipment clock hours, operational performance and operating events (where an “event” is defined as any off-normal condition of the equipment). Therefore, an event can be an equipment unplanned forced outage, underperformance or fault.
It is important that every asset’s performance is monitored and that failure categorization is automatically assigned by the system. This data, when associated with the EAM maintenance data, will provide the information needed to calculate the equivalent operating hours of the equipment.
Our goal is to understand the relationship between equipment operating duty and equivalent operating hours. One clock hour of operation is equal to one equivalent hour of operation when we are running the asset at its guarantee conditions. Any deviation in operating duty from guaranteed operating conditions can result in an equivalent operating hour of more or less than the actual clock hours the equipment ran.
To calculate equivalent operating hours, we need at least the following information:
- Equipment clock hours of operation
- Storage system c-rate, cycles, module temperature, depth of discharge
- Equipment failure data, including: unit availability, forced outage rate, mean-time-between-failure and failure category, cause and action taken
- Maintenance performed because of equipment failures
It should be apparent from the above that monitoring system reliability data must be associated with the maintenance and repair activity data and costs if we are going to characterize the relationship between an equivalent operating hour and O&M costs.
FINANCIAL SYSTEM DATA
A third key data platform that should be integrated with monitoring and maintenance data is O&M cost data from the financial system. Most organizations consider their financial system as the system of record for unit price data such as the cost of field technician labor or the price of a fuse.
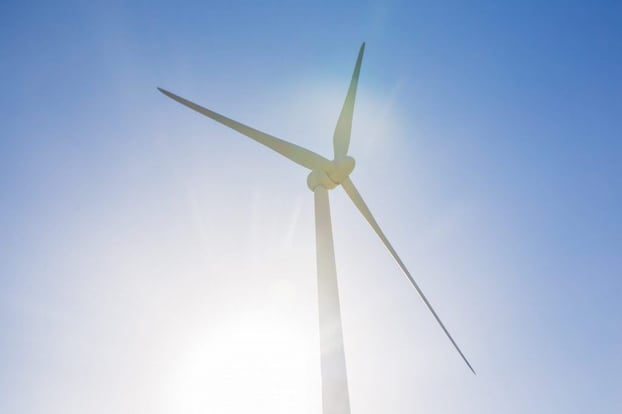
To calculate operating costs, we need to marry the quantities of technician hours and fuses replaced with their unit price data stored in the financial system. Therefore, a good EAM will include a bi-directional interface to the customer’s financial system so this data can be seamlessly shared between the two systems.
Because we want to characterize detailed asset operating costs with operating duty and equivalent operating hours, it is important that the EAM and financial system have a mapped asset registry and link the work order number to the specific cost incurred for each maintenance and repair activity.
Financial system data that is needed to calculate asset operating costs, include:
- Labor, materials, and other maintenance activity unit prices and actual costs
- Work order associated with the cost
- Asset associated with the cost
COMMERCIAL ASSET MANAGEMENT SYSTEM DATA
The final data platform that should be integrated in the APM platform is the commercial asset management (CAM) system. The CAM is the system of record for managing renewable power asset contracts, including power purchase agreements, supply agreements, O&M agreements and warranties.
Though CAM data is not used directly to calculate equipment operating costs or equivalent operating hours, it stores all the contractual terms and context (metadata) related to these costs. In addition, a good CAM can trigger event-based compliance notifications, such as warranty events, alerting asset managers that warranty claims against a specific supplier should be filed.
Commercial asset management data should include the following:
- Supply agreements
- O&M agreements
- Warranty terms
- Performance guarantees, including guaranteed operating conditions and specifications
PULLING THE INFORMATION TOGETHER
Though this article is not meant to be an exhaustive specification for integrating these four data systems together, it should be apparent that the integration layer must include at least the following features:
- Common asset registry: All four systems need to share a common asset registry so that maintenance and repair activity and costs can be tracked by asset and operating duty.
- Metadata exchange: The APM should be the system of record for the asset registry, however, asset meta data exchange should be bi-directional. For example, if the financial system is where supplier contact information is managed, the EAM registry should be updated when a site’s O&M contractor is replaced in the financial system.
- Standard failure code taxonomy: A standardized failure taxonomy should be implemented in the EAM, and failure data should be exchanged between the event engine and the maintenance system.
- Event engine: The APM event engine must communicate with all other data systems so both technical and commercial operating events can be managed and triggered. This means the APM architecture must include a universal event messaging bus so event producers and consumers can easily pass information from system to system.
There is much more to discuss on this topic, but I’ll save that for a future article.
Drive O&M and Drive APM work together to empower teams with a condition-based maintenance solution that’s purpose-built for renewables.
Interested in learning more? Download the Drive O&M brochure.
FEEDING THE RESULTS INTO YOUR ECONOMIC MODEL
I mentioned in the first article of this series that the storage asset class, because of its ability to arbitrage energy, introduces additional uncertainty and risk into the renewable power portfolio. Since real-time power prices are constantly changing and cannot be predicted with certainty, any energy storage system that can participate in real-time markets can’t really know in advance what the kind of operating duty the system will experience over time.
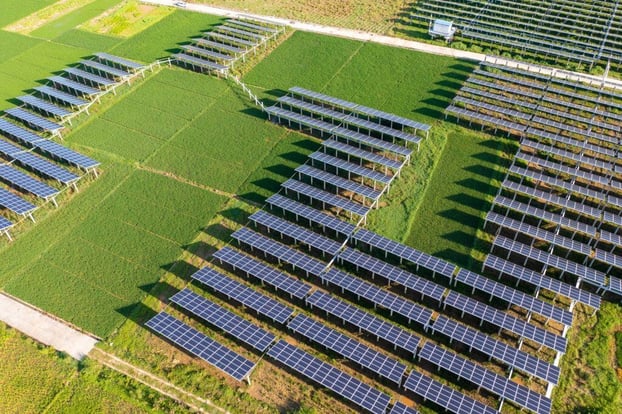
Because of this reality, asset managers and scheduling coordinators will need to frequently update the project economic model with more accurate cost and asset life estimates. Where do some of these important model input assumptions come from? The asset performance management platform.
Therefore, asset performance and costs metrics – such as round-trip efficiency, capacity fade rates, estimate useful life and operating costs – need to be available as KPIs in the system and regularly refreshed in the project performance model and economic dispatch model.
I would recommend that these values be updated monthly if the storage system is experiencing a lot of cycling – especially if the storage system is not operating closely to the original design or guaranteed operating conditions in the supplier specifications.
SUMMARY
The introduction of the storage asset class brings new complexity to the renewable power asset owner. To properly understand the variable operating costs of an asset class with potentially changing operating duties, it is important that all the data systems that manage performance, cost and maintenance are integrated so asset managers have the best information possible when scheduling storage assets into the market.
In the next article, we’ll talk about how to maintain an integrated data platform that provides an accurate assessment of asset economic life.
Now retired, Steve Hanawalt co-founded Power Factors in 2013 and spent almost 40 years in the energy industry. For more renewables industry content, follow Power Factors on LinkedIn and Twitter.