Myth #3 of Solar O&M: Break/Fix is the Best Maintenance Strategy
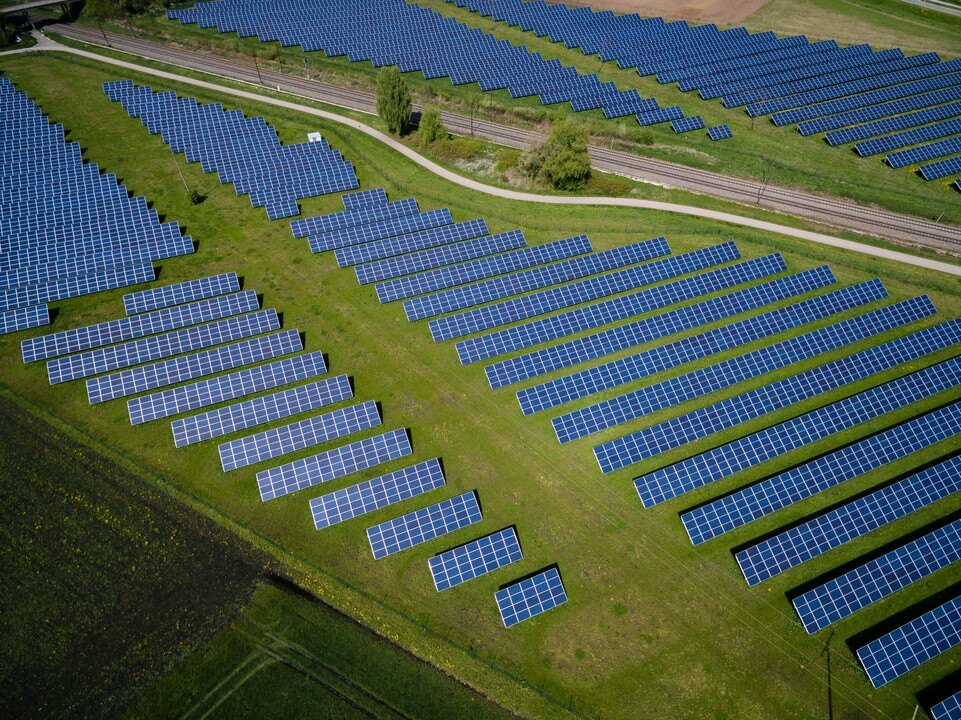
Stay in touch
Subscribe to our newsletter for expert insights, company updates, and the latest in renewable energy management solutions.
In my early days as vice president of O&M for a large developer, I overheard one of our salespeople telling a prospective customer that our solar power systems didn’t need to be maintained. When I pushed back, they said, “OK, maybe some maintenance is required, but a break/fix maintenance plan should be more than sufficient.” My guess is that this same person routinely changed their car’s oil every 3000 miles. Why would a multimillion-dollar solar asset not deserve the same treatment?
A break/fix maintenance strategy isn’t a maintenance strategy; it’s a spares replacement strategy.
In break/fix, we wait until a part breaks or a device is no longer serviceable, then we replace it. Changing a light bulb is the classic break/fix maintenance approach — when one bulb fails, you simply pull a new one off the shelf. A break/fix maintenance strategy really isn’t a maintenance strategy at all; it’s a spares replacement strategy.
For light bulbs and other low-cost, low-impact consumables, a break/fix maintenance plan works. Typically, the failure of a light bulb doesn’t reduce the facility’s generating capability or pose a safety threat. Light bulbs are cheap and readily available. Have a few on hand, and you’ll probably be fine.
The best maintenance strategy is the one that contributes to the lowest levelized cost of energy (LCOE) for your facility.
A far superior maintenance strategy, however, is the one that contributes to the lowest levelized cost of energy (LCOE) for your facility. Usually, the best maintenance strategy is a hybrid or integrated strategy that includes break/fix, preventive, and condition-based maintenance practices.
MAINTENANCE STRATEGY OPTIONS
Let’s review each of these, briefly, in order:
BREAK/FIX
As described above, a break/fix approach should only be assigned to low-cost, highly-available consumables such as light bulbs and fuses. Typically, these devices don’t have any sensors so it’s difficult to monitor their health and predict their failure rate. For some key fuses where loss of production would result from a failure, a preventive maintenance strategy may be prudent.
How do I know when to shift from a break/fix to a preventive or condition-based maintenance strategy? When the current strategy has a negative material impact on your project LCOE.
PREVENTIVE
Preventive, or planned, maintenance, can be compared to going to the dentist every six months for a checkup. As far as you know, all is well with your teeth, but the consequences of catching a problem too late (break/fix) is too painful or costly to make skipping that regular checkup a good idea.
Preventive maintenance performs equipment maintenance at regular intervals following standard procedures. Some useful life of the part invariably is sacrificed when we use preventive maintenance as a maintenance strategy.
CONDITION-BASED
Condition-based maintenance relies on real-time monitoring of key operational parameters of a device to determine the equipment’s current condition. For example, we might measure inverter heat sink and ambient temperature and correlate them to inverter current. If we see asignificant deviation from expected, it could be due to an imminent IGBT failure. We shut the unit down and perform further investigation and analysis.
A break/fix maintenance strategy would have allowed the IGBT to fail, then fixed it. A preventive maintenance strategy would have replaced the IGBT at some calendar interval — too late and we have a break/fix issue on our hands; too early and we aren’t extracting all of the value from the device before we replace it.
In a perfect world where we have unlimited time, money, and resources, all maintenance would be condition-based. Every asset would experience its full economic life and our maintenance cost contribution to plant LCOE would be optimized. Unfortunately, we live in a world of scarcity, so an exclusive, condition-based maintenance program for a solar plant doesn’t make sense. As outlined above, a hybrid maintenance strategy wins.
How do I determine which of the plant’s maintenance activities should be break/fix vs. preventive vs. condition-based?
WHICH HYBRID STRATEGY?
The right hybrid maintenance strategy delivers the optimal (note: not lowest) maintenance spend. The optimal spend will result in the lowest LCOE for the plant. How do I determine which of the plant’s maintenance activities should be break/fix vs. preventive vs. condition-based? Of course, I can’t answer that question for you, because it depends.
The only right way to determine which maintenance activities should follow which strategy is to build an economic model. The model will need to estimate failure rates, parts costs, replacement times, and the opportunity cost of an outage. It likely will need to start with gross assumptions until some real-world operating data becomes available and/or if you can obtain mean-time-between-failure (MTBF) data from your OEMs.
Only you and your maintenance team can determine what is the best strategy for your portfolio of assets. That said, here are some rules of thumb:
- Low-cost, easily-available parts where local maintenance techs are available will probably be best maintained using a break/fix strategy.
- Moderate-cost, moderately-available parts with regional maintenance providers may be best-suited for a preventive maintenance strategy.
- High-cost, hard-to-find parts only replaced by specialist maintenance technicians will probably be best served by a condition-based maintenance program.
So next time someone says, “Break/fix is the right maintenance strategy,” enlighten them by responding, “…sure, as long as it’s in combination with a preventive and condition-based maintenance plan.”
Steve Hanawalt is a founder and executive vice president at Power Factors.